Servomotors and Managing Current
CS
480: Robotics & 3D Printing Lecture, Dr. Lawlor
Interfacing with R/C Servos
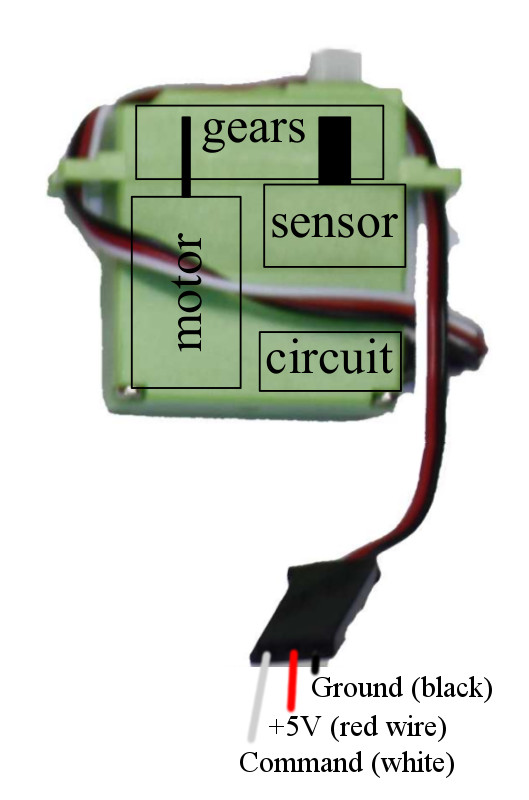
An R/C servo is an inexpensive (about $10) device that includes a DC
motor, geartrain to increase the motor's effective torque, and a
position sensor that allows you to command the position of the
output shaft. They're frequently used for small robot arm and
gripper tasks.
In class, we demonstrated a clone of the MG995, a heavier duty servo
with metal gears. Like all common servos, it takes a 1-2
millisecond command pulse on the white wire to specify the desired
angle of the output shaft, from 0-180 degrees.
#include <Servo.h>
Servo s;
void setup() {
Serial.begin(9600);
Serial.println("Enter angle in degrees");
s.attach(8);
}
void loop() {
if (Serial.available()) {
int i=Serial.parseInt();
if (i>0) {
Serial.print("Seeking to position ");
Serial.println(i);
s.write(i);
}
}
}
Servo Size
There doesn't seem to be any truly standard sizes for servos,
although they all have similar proportions, and the midrange 40.5mm
x 20mm profile is nearly standard. There's a searchable database of servos
on the market today.
Style
|
Length / overall
|
Thickness
|
Height / overall
|
Diameter of output shaft
|
Mass
|
Rated torque/speed
|
Speed to track 60 degrees
|
Voltage
|
"Giant" (Hitec HS-805BB)
|
65.8
|
30
|
57.4
|
10mm
|
153g
|
20 / 25 kg-cm
|
0.19 / 0.14
|
4.8 / 6.0 volts |
"Standard"
(MG995 or MG946)
|
40.5 / 54 mm
|
20mm
|
28.5 / 43.5 mm
|
5.9mm
|
50g
|
10 / 15 kg-cm
|
0.18 / 0.16 seconds
|
4.8 / 6.0 volts
|
"Mini"
|
28.8 / 40.44 mm
|
13.5mm
|
22 / 36.5 mm
|
5.7mm
|
20g
|
5 / 6 kg-cm
|
0.20 / 0.16 seconds
|
4.8 / 6.0 volts
|
"Ultra micro" (HK-5320)
|
13.5 / 20 mm
|
6.3mm
|
10.5 / 18.9 mm
|
2.9mm
|
3g
|
0.05 / 0.075 kg-cm
|
0.07/0.05 seconds
|
2.8/4.2 volts
|
Current Distribution
One recurring issue in robotics is reliably supplying enough current
to drive your motors--big DC motors are some of the most
current-hungry and electrically noisy devices available today.
In class, we showed how an Arduino can reliably command an MG995
servo for short distances, but long-distance rapid moves cause
enough electrical disturbance to reboot the Arduino when the servo
is drawing its power through the Arduino's 5V regulator.
The solution is to add a current supply capable of sourcing more
amps, such as a Lithium-Polymer
(lipo) battery. If you pull out one cell (3.5-4.2
volts), for example via the battery
balance pins, you can wire this directly to the servo's red
+5V input, as long as you have a shared ground connection.
More generally, for large robots supplying and distributing
sufficient electrical current can be challenging, requiring thick
wires or even solid conductor bus bars. For our robot mining
robot, we run solid aluminum channel from the battery bus to supply
the motor controllers, which stall at 40 amps per motor!